Our experience
WE SUPPORT
FACTORIES
WE HAVE
INTEGRATED
PRODUCTION
LINES
WE HAVE
IMPLEMENTED
APPLICATIONS
WE WORK FOR
INDUSTRIES
Our customers
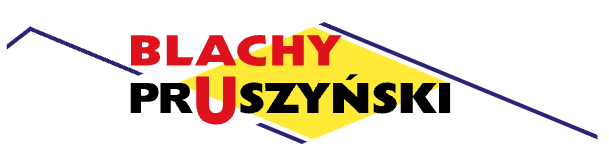
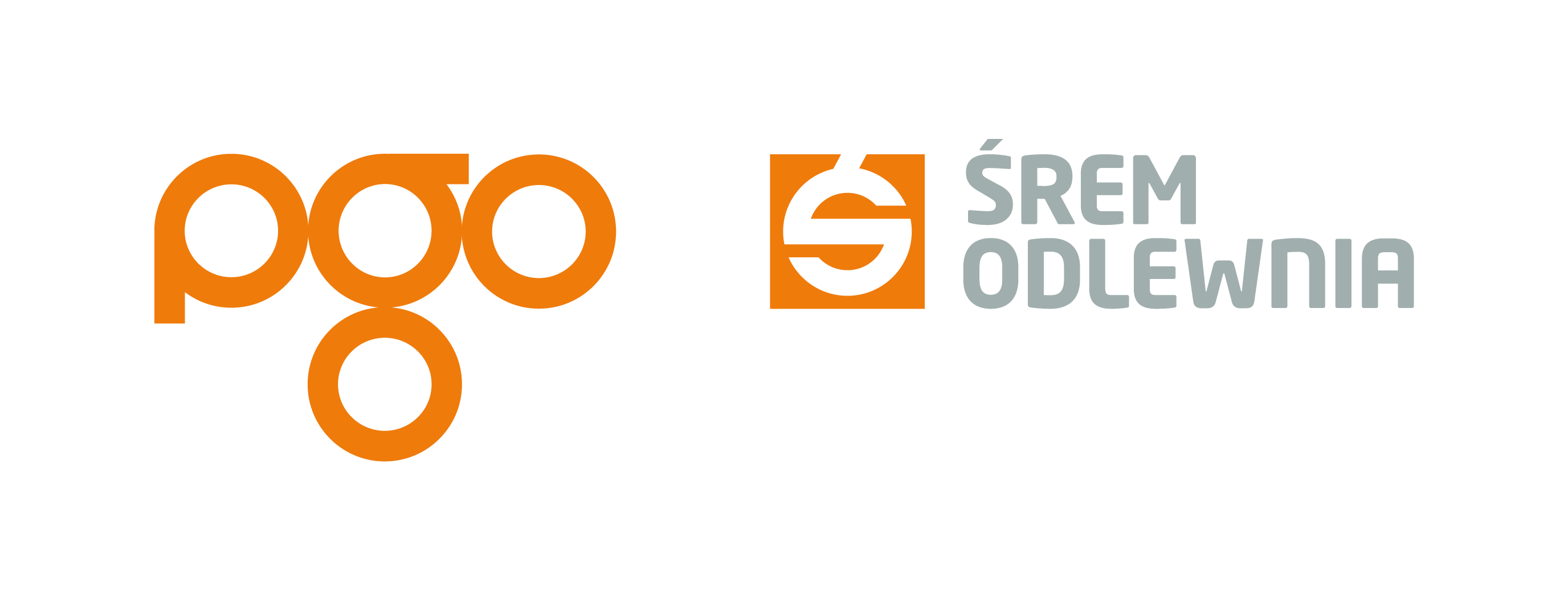

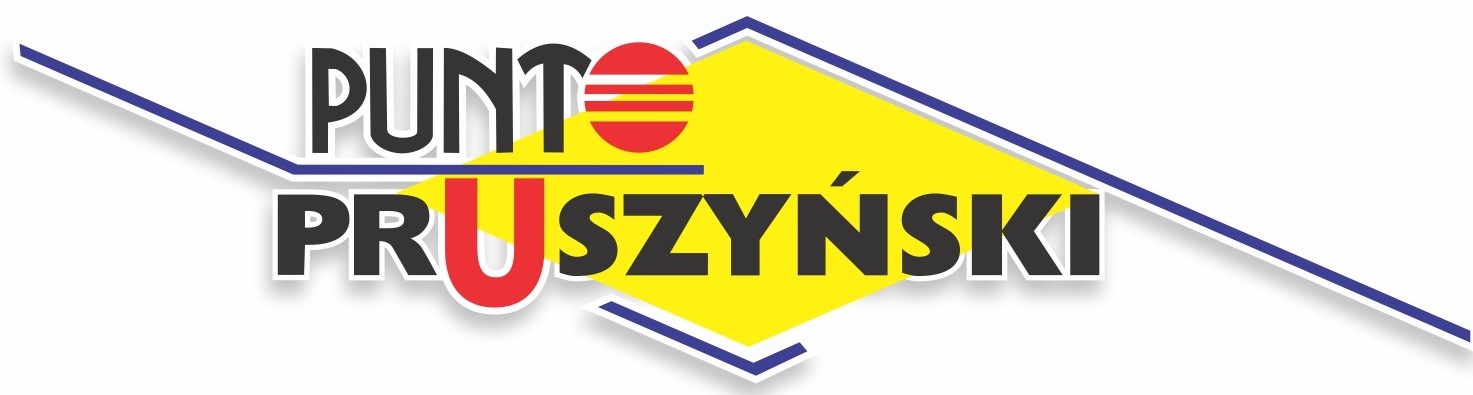

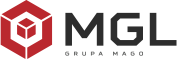
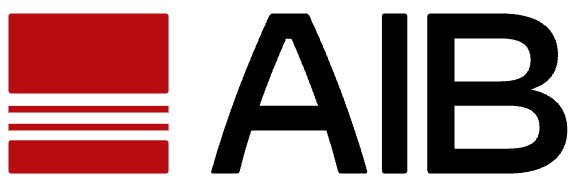
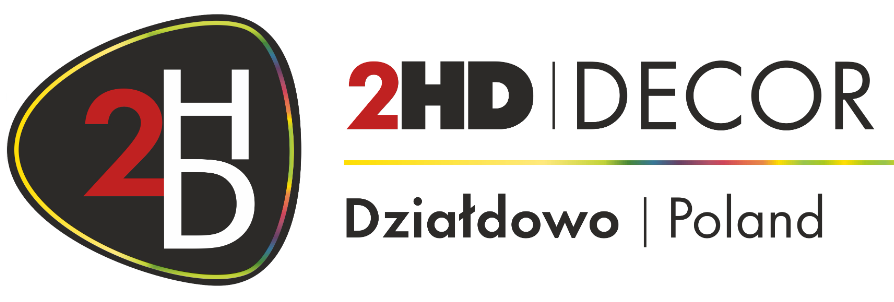
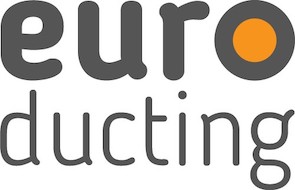

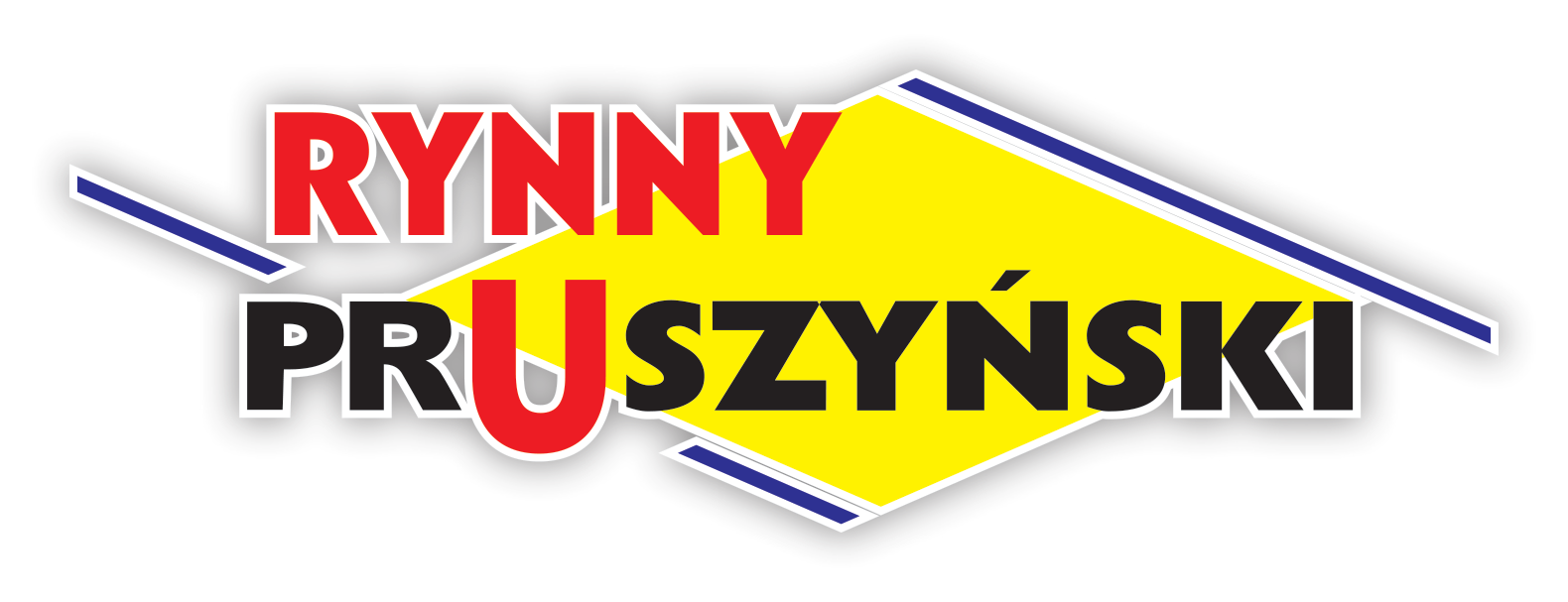
What they say about us
SMART TRADING COMPANY
“(...) It is important to emphasize the great commitment of STABILIS.IO employees as well as very good communication.”
Konrad Nowak - Ignatowski
Managing Director & CEO
2HD DEKOR
“(...) Our cooperation ran smoothly and with great commitment, which is why I wholeheartedly recommend STABILIS.IO as a specialist in its industry and a reliable and trustworthy business partner.
Janusz Żyznowski
COO
GRUPA PRUSZYŃSKI
“(...) Cooperation with STABILIS.IO was very professional and without delays, and the delivered product meets the highest quality criteria required by the Pruszński Group.”
Paweł Duszczyk
Director of the IT Department
Our partners
STABILIS® systems harness data from a broad array of IoT solutions provided by Sigfox Poland.
As a provider leveraging the global 0G network accessible in over 70 countries, our mission is to unlock the potential of businesses through data. Sigfox services include digital connectivity for IoT devices, LPWAN technology, and applications designed to generate digital twins of business processes in sectors such as transportation, logistics, manufacturing, and building management.
STABILIS® systems in industrial facilities run on dependable Advantech IPC computers.
Advantech is a global leader in Internet of Things solutions, offering innovative products and services that propel digital transformation across various industries. With cutting-edge technologies and deep expertise in IoT, Advantech enables customers around the world to effectively implement smart solutions, supporting their business success.